McKee, Paul. "Maryville University New Residence Hall Grading.” 2015. JPEG File.


Foundational Information
-
Paul J. McKee IV
-
Superintendent Intern
-
77 Westport Plaza, Suite 250 St. Louis, MO 63146
-
Main: (636) 561-9500
-
Direct: (636) 561-9857
-
Email: pjmckeeiv@paric.com
-
-
Paric Corporation
-
77 Westport Plaza, Suite 250 St. Louis, MO 63146
-
(636) 561-9500
-
-
Mike Rozier
-
Overview of Company
-
Commercial Construction Company
-
Around 300+ employees
-
$315,000,000 in work for 2015
-
Paric, founded in 1979 and based in St. Louis, Missouri, is one of the largest privately held companies in the Midwest. Paric is a leading general contractor, construction manager and design-build firm in the St. Louis region. The company specializes in senior living, healthcare, historic renovation and the City of St. Louis, hospitality and multi-family residential, public and academic, as well as interior specialty projects. Paric manages construction projects for long-term and repeat clients ranging from universities and banks to hotels, restaurants, warehouses and trade centers.
-
Wix.com. "Stock Photo.” 2015. JPEG File.

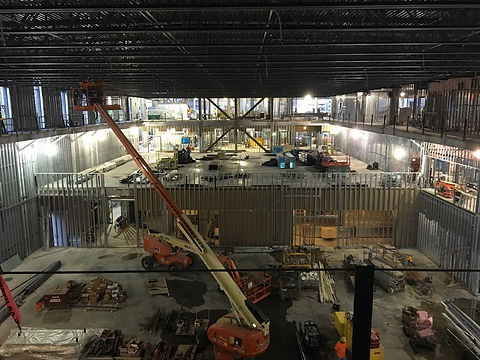

Weekly Reports
-
Week Ending 5/6/16 – 40 hours worked
-
Company and Site orientation. Erection of 1st-2nd floor steel on east wing as well as metal decking on top. Decks prepared for future concrete pours. Second floor west side concrete poured and finished. Interior mockup completed and documented. Weekly safety orientation, daily updates, safety surveys, PM meeting, and Foreman meeting.
-
-
Week Ending 5/13/16 – 40 hours worked
-
Competition gym structural stud wall installed, Steel erection on east wing up to third floor continued, Gym roof joists installed, roof and floor metal decking installed. First floor stud wall installation started. Rain causing major setbacks and delays. Weekly safety orientation, daily updates, safety surveys, PM meeting, and Foreman meeting.
-
-
Week Ending 5/20/16 – 40 hours worked
-
MEPFP rough-in continues in the gym and first floor area. Intermural gym floor prepped for concrete pour. Steel erection continued. Roof drain piping installed, second floor framing and topping out started. Weekly safety orientation, daily updates, safety surveys, PM meeting, and Foreman meeting.
-
-
Week Ending 5/27/16 – 40 hours worked
-
Intermural gym floor concrete poured. Visited hollow core panel production plant to observe material for our job being made. Roof and third floor metal decking continued. Steel erection on the east skew line continued. Weekly safety orientation, daily updates, safety surveys, PM meeting, and Foreman meeting.
-
-
Week Ending 6/3/16 – 40 hours worked
-
First floor locker room block walls started. Second crane arrived on site two steel raising gangs working on east skew line. Lots of rain delaying the job. Weekly safety orientation, daily updates, safety surveys, PM meeting, and Foreman meeting.
-
-
Week Ending 6/10/16 – 40 hours worked
-
Fireproofing of first and second floor began, Hollow core panels started, Framing of gym walls started, Topping out of priority walls continued, Steel erection going full speed, deck prep for concrete pours continuing, MEPFP’s continuing behind framing and topping out. Weekly safety orientation, daily updates, safety surveys, PM meeting, and Foreman meeting.
-
-
Week Ending 6/17/16 – 40 hours worked
-
Steel erection and metal decking continuing, second floor deck pour and first floor slab on grade pour back in gym area. Tilt up panel painting and caulking, locker room block walls continuing. Weekly safety orientation, daily updates, safety surveys, PM meeting, and Foreman meeting.
-
-
Week Ending 6/24/16 – 40 hours worked
-
Steel erection up to 7th floor on south skew line, third floor deck pour, deck prep for other pours, MEPFP continuation, fireproofing continued, chiller lines started being installed, chiller and fire system pumps delivered. Weekly safety orientation, daily updates, safety surveys, PM meeting, and Foreman meeting.
-
-
Week Ending 7/1/16 – 40 hours worked
-
Continued installation of hollow core panels, second floor remaining deck pour, structural steel/decking/joist installation, framing and MEPFP continuation, completion of first floor locker room CMU walls, painting and patching of tilt up panels, Weekly safety orientation, daily updates, safety surveys, PM meeting, and Foreman meeting.
-
-
Week Ending 7/8/16 – 40 hours worked
-
Low rise TPO roofing started on competition and intermural gym room, Stair one and two set, fireproofing started once again on third floor, erecting steel up to floor 7 on south skew line, continued installation and welding of hollow core panels, Weekly safety orientation, daily updates, safety surveys, PM meeting, and Foreman meeting.
-
-
Week Ending 7/15/16 – 40 hours worked
-
Site utilities finished, roof drain bubblers and grease trap installed, loading dock and north delivery road brought to grade, fourth floor concrete deck pour finished, fourth floor concrete stem wall poured, first floor dining hall MEPFP’s and framing started, Air handler units delivered, Weekly safety orientation, daily updates, safety surveys, PM meeting, and Foreman meeting.
-
-
Week Ending 7/22/16 – 40 hours worked
-
Second floor CMU block walls started, Tilt up panel punch windows installed, Curtain wall drop down steel and bottom track installed, Chiller pads installed, third and fourth floor framing and topping out, Air handlers installed, exterior framing started, hollow core install finished up to 7th floor on south wing, 4th floor fireproofing completed, MEPFP’s installing priority lines and systems on all floors, All gym wiring pulled, end of internship presentation to exec. board, weekly safety orientation, daily updates, safety surveys, PM meeting, and Foreman meeting.
-
End of Internship Report
Contents:
-
General Information
-
Relationship of Work Experience to CSM Curriculum
-
Problem and Solution
-
Ethical Situation
1. General Info
Internship Duration: 5/2/16 – 7/22/16
Total Hours Worked: 480
For my internship during the summer of 2016 I had the opportunity to work as a Superintendent Intern for Paric Corporation in St. Louis, Missouri. I was assigned to the St. Louis College of Pharmacy Phase II, this was a 7 story multi-use facility that included 2 competition gyms, workout facilities, a dining hall, faculty offices, and student dorms. I was assistant to a Senior Superintendent and spent my summer dealing with site logistics, safety, quality, and scheduling different trades. Being a superintendent, I got to be on site 100% of my days and got to know the ins and outs of all methods being used. From hollow core panels to architectural precast panels I had the unique opportunity to see manufacturing processes and installation methods furthering my construction knowledge for my future in the industry.
2. Relationship of Work Experience to CSM Curriculum
The first four floors of the job I was on this summer were all deck pours. After the first four floors, the next three were structural steel with hollow core pre-stressed panels welded on top. Thanks to CSM 203 and 205 this was not the first time I have heard of this building material and the method used to manufacture and install these hollow core panels. What made getting to work with these panels even better was the opportunity I had to visit the plant that was manufacturing them. I was able to explain the whole process and applications to the owners’ representative and architects thanks to what I had learned in my Materials & Methods classes. In addition to knowing the manufacturing process when it came time to start installing these panels on site, we had to cut a few to fit. When cutting hollow core panels it is important to know how they have their strength from the pre-stressed cables, and if one is cut the entire strength of the panel is compromised. Thanks to my understanding of this method, I was able to direct the workers to cut away from the cables to avoid destroying the panels. This is just one example of the hundreds of materials and methods I saw this past summer so it is safe to say that this class helped me do my job and so much more.
During the second half of the summer, a discrepancy was noticed on the architectural plans. The running track around the third floor above both gyms was designed to have a drywall and glass handrail. An engineer did not design this rail in the plans and had nothing in the specifications. The problem was that this rail needed to be a structural element, as it is required to hold a certain force to prevent runners from falling through it. The architect on the job skirted responsibility by saying it needed to be designed to the standard for handrails. Unfortunately, for us our drywall and framing sub did not catch this and had not accounted for it in their bid. With the skills, I learned in CSM 204 on how to read contract documents and drawings I was able to help the project team solve this problem. I had to run through multiple contracts and specifications to see who had accounted for this guardrail and once we discovered that it was not accounted for we had to find a solution. This required extra reinforcing to be placed along the rail perimeter before we poured the deck slab. In order to do this I had to reference the plans and scale the perimeter of the track in order to find the proper spacing of the reinforcement. Without the knowledge, I learned in both the class and lab of contract documents I would not have been very helpful in solving this problem.
A large part of my summer was helping to manage our large and varied workforce on site. When I say varied, I mean we had multiple trades who had many minorities and women working for them. With such a diverse workforce on our site, I ran into several situations where I needed to change my approach on talking to certain people and getting them to complete tasks. The skills I learned in MGT 307 where very helpful in management of our jobs human resources. One glaring example came toward the end of summer when we had a near miss accident involving a crane operator and multiple ironworkers. After this incident, the company safety director instructed me to conduct an investigation as to the events that led up to the incident and to collect stories from all that were involved. The skills I learned in MGT 307 had taught me how to handle situations with this. The key when talking with multiple people about the same event is to remain as unbiased as possible and avoid making judgments until all information has been gathered. Another big aspect is the punishment for the guilty parties, It is important to not always punish for certain things but rather to make it into a learning experience to build off of and that is exactly what we as the GC did in order to try and prevent future accidents of the same type. Without the knowledge I had gained about human resources I would not have been very helpful making this bad situation into a positive.
3. Problem and Solution: explained below
While working on the St. Louis College of Pharmacy for Paric Corporation it was discovered that multiple beams between the steel frame and tiltup panels were fabricated too long due to a misunderstanding of the measurements on the Structural Drawings.
Problem: Multiple steel beams were fabricated in the wrong length due to a misreading of plans
Step One: Signals a Problem Exsisted
-
Continued issues and difficulty installing beams between steel frame and tiltup walls
-
Issues were unknown by the design team or the subcontractors
-
All parties were unaware of issues until installation
-
Structural plans were difficult to pick up correct dimensions from
Step Two: Problem Assumptions
WHAT- Steel beams were wrong dimensions, all should have been fabricated according to structural plans
WHERE- The north side of the building connecting the steel frame to the tiltup panels
WHEN- Observed by ironworkers when they attempted to install beams
WHO- Design Team, Steel Fabricator, Subcontractors, Project Team
TO WHAT EXTENT – Around 20 steel beams around 30ft in length needed to be field modified to fit
Step Three: Interpreting Assumptions
Facts- Steel beams were fabricated too long
Assumptions- Beams need to fit so construction can continue
Expressions of Frustration- This should not be a mistake, plans aren't hard to read
Expressions of Blame- If the fabricator and structural engineer would have communicated we would not have a problem
“Knee-jerk Solution"- We will make the beams fit no matter what to keep construction going
Step Four: Problem Stated With Facts Only
The structural plans require these beams to be the right length to carry the building load . We need to follow these plans
Step Five: How to Eliminate the Problem in the Future
I will immediately begin to find a solution to shorten the beams; as I work on other jobs in the future I will ensure that the Engineer and Fabricator are on the same page before steel production.
Step Six: Alternate Solutions
-
Send the beams back to the fabricator to be refabricated in the correct dimensions
-
Cut and slot the beams in the field to the proper dimensions
-
Find a local fabricator that can try and replace the wrong beams quickly
Step Seven: Ranking Alternates
Alternate 2: This is the quickest and easiest solution when trying to keep the job on schedule but will cost the fabricator a lot more money when it comes to paying for extra man-hours
Alternate 3: A possible solution if a fabricator can be found that is not too busy. Would be very costly but quicker than Alternate 1
Alternate 1: The most costly and time consuming solution due to the fabricator being in Mississippi.
Step Eight & Nine: Problem Solution
Due to the schedule, already being super tight we had to field modify the beams and get them approved by the structural engineer to keep the job on track. It still held the job up for a work week and cost a lot of overtime hours but in the end it was worth the grief because the duration was still less than the other two options. If we ran into this problem, again I don’t see doing anything differently. The only thing that could possible change my mind was the location of the fabricator and their lead-time to make new beams. They were part of the critical path in our schedule and without a quick fix we could have easily been pushed back weeks losing even more money all because of a few inches.
4. Ethical Situation: explained below
This past summer at the St. Louis College of Pharmacy, we had many challenges and ethical situations. The one downside to being on a large job is that not everything can go as planned and sometimes you must improvise for the betterment of the job. One such issue we ran into this past summer had to do with completing work to move the schedule without getting the needed sign offs from the respective inspectors. Sometimes we as a project team found it necessary to continue building instead of waiting on a city inspector to show up. Sometimes this worked out in our favor with him being ok with our continuation but outer times led to us being reprimanded and being told to fix the issues. One such issue had to do with structural steel connections and the fact that not all bolts were in place when addition steel was added on top and while the concrete decks were poured.
This specific example was due to us needing to get more steel up vs. us needing to put all of the bolts in. The steel frame was in the middle of our critical path and the bolts were not it was a simple decision. While this did not affect the structure of the building or the safety of any workers it was still and unsafe situation. While all bolts were eventually added it did not mean the city inspector did not reprimand us. In some places, we had to remove fireproofing and concrete to get bolts in. This type of situation occurred several times over the summer but were never so bad that anything major was at risk other than money. While they were not ethical practices, they were practical and the project team approached them as such.
-
Knowing that if you wait for signoffs on every little thing you will never get anywhere on the job. Therefore, you decide to risk damage to the building and losing money all in an attempt to stay on schedule. Because these are such small problems, the consequences are not as bad as they could be and encouraged the project team to continue on this fine line.
-
As a reputable contractor, it is your right to push certain things in order to keep to the schedule but at the same time, it is also your responsibility to ensure the safety of all workers and future occupants of the building by making sure everything is constructed as designed. Therefore, it is your duty to not skip any steps and find other less dangerous ways to make up time on your schedule.
-
In this given situation, a good person would most certainly stop working so far ahead of inspections. A dangerous and pointless practice can be fixed with more attention to details and communication with the inspector. Corners can be cut but you must know what the right ones to cut are.
McKee, Paul. "St. Louis College of Pharmacy Phase II.” 2016. JPEG File.
McKee, Paul. "St. Louis College of Pharmacy Phase II.” 2016. JPEG File.
McKee, Paul. "St. Louis College of Pharmacy Phase II.” 2016. JPEG File.
McKee, Paul. "St. Louis College of Pharmacy Phase II.” 2016. JPEG File.
McKee, Paul. "St. Louis College of Pharmacy Phase II.” 2016. JPEG File.